A process furnace is typically defined as an industrial furnace that uses heat to produce chemical and state changes in materials. The heating mechanism can be direct-fired where the material is in contact or close proximity to combustible fuel, or indirect-fired where the heat is carried by an exchanger to the material to be heated. Process furnace designs often use coal, oil, or a mixture of combustible gasses as a fuel source. They are built for a variety of applications including annealing, brazing, and carburizing materials.
Brazing is a method for joining two types of materials that have a high melting point by mixing them with a molten filler metal of a lower melting point in a process furnace. The two main types of process furnace design used for brazing are retort and vacuum chamber furnaces. Retort furnaces incorporate hydrogen gas to clean the brazed components. Vacuum chamber brazing is used where a highly purified material is desired, and furnace temperatures can reach 3,002° Fahrenheit (1,650° Celsius). High strength and corrosion-resistant metal alloys for aerospace engine components and electronics are produced by brazing, and filler metals used include silver and copper, or more often nickel and gold.
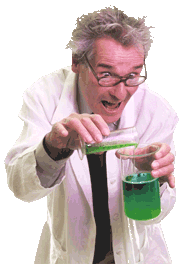
The carburizing process furnace is used to treat alloys of steel by introducing more carbon into it, which increases its surface hardness and durability. It operates by infusing the furnace chamber's atmosphere with carbon compounds that diffuse into the surface layers of the steel at a temperature between 1,508-1,724° Fahrenheit (820-940° Celsius). The carburizing cycle typically takes several hours per batch of material.
An annealing process furnace heat treats materials to remove mechanical strain and oxidation. They typically operate in temperature ranges from 932° Fahrenheit (500° Celsius) to remove metal strain, to 1,220° Fahrenheit (660° Celsius) to remove oxides. The range of temperature of an annealing furnace is fully programmable for unique jobs and materials, within an accuracy level of plus or minus 4.1° Fahrenheit (0.5° Celsius). Their full operating range is from 572-2,012° Fahrenheit (300–1,100° Celsius).
Several other types of process furnace designs exist, including the electrical arc furnace, blast furnace, and induction furnace. The electric arc process furnace is most often used to produce cast iron and refine steel. Blast furnaces are used to smelt and purify a wide variety of metals from iron to copper and gold. Induction furnaces use the principle of electrical induction produced by changes from high voltage to low voltage current as a heat source. They are widely used to melt and alloy a range of both ferrous iron and steel, and non-ferrous metals.